- Overview
- Product Description
- Product Parameters
- Detailed Photos
- Our Advantages
- Packaging & Shipping
- Certifications
- Successful Project
- Related products
Basic Info.
Product Description
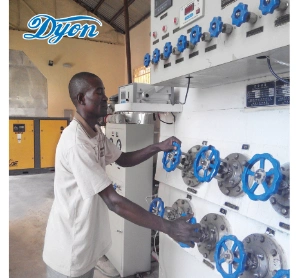
Differ from Pressure swing adsorption process (PSA) process, we adopt Cryogenic distillation process for making the air separation plant.
With this process, pure gases can be separated from air by first cooling it until it liquefies, then selectively distilling the components at their various boiling temperatures. It can produce high purity gas product.
Specification for cryogenice oxygen plant | |||
Design condition | Atmospheric pressure | mmHg | 760 |
Ambient temperature | ºC | 32 | |
Relative humidity | % | 75 | |
Main performance parameters | Oxygen output | Nm3/h | As user's requirement |
Oxygen purity | % | 99.6 | |
Working pressure | Mpa | Subject to the final design | |
Power supply | Voltage | V | 380/220 (Subject to user's condition) |
Frequency | Hz | 50(Subject to user's condition) | |
Total power consumption | KW | Subject to the final design |
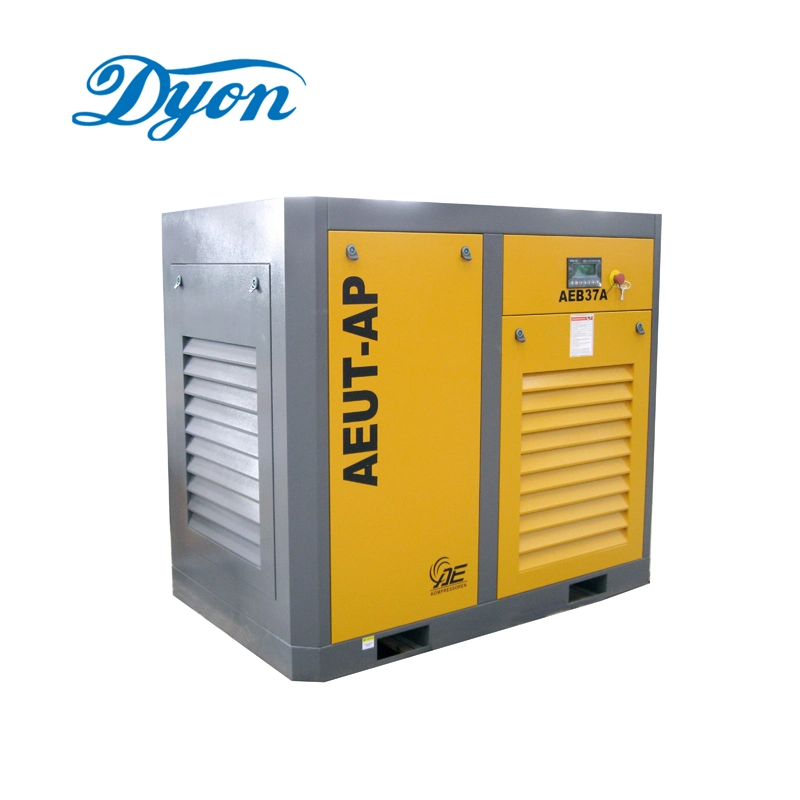
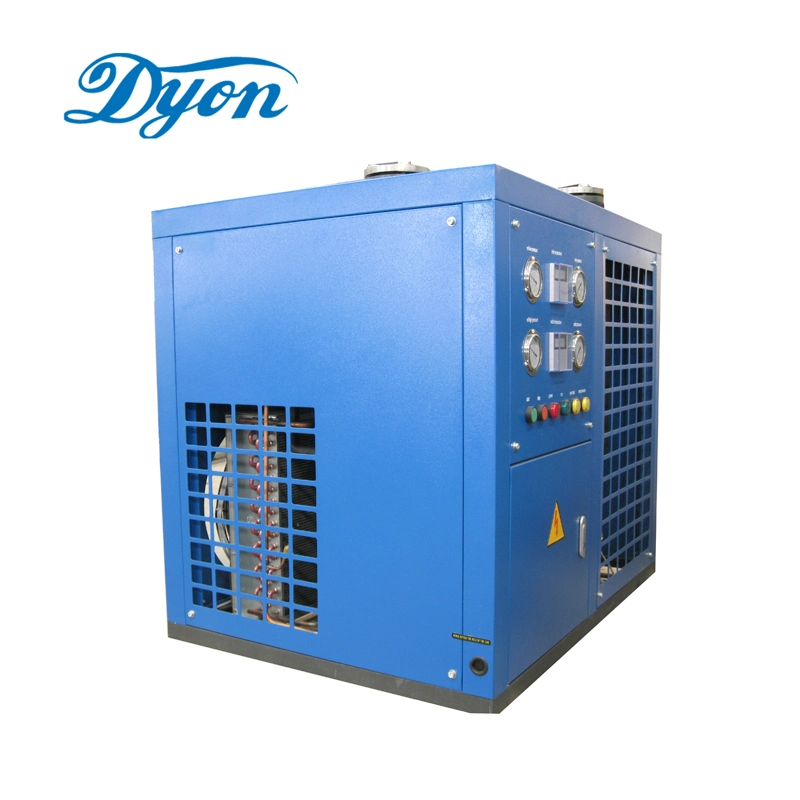
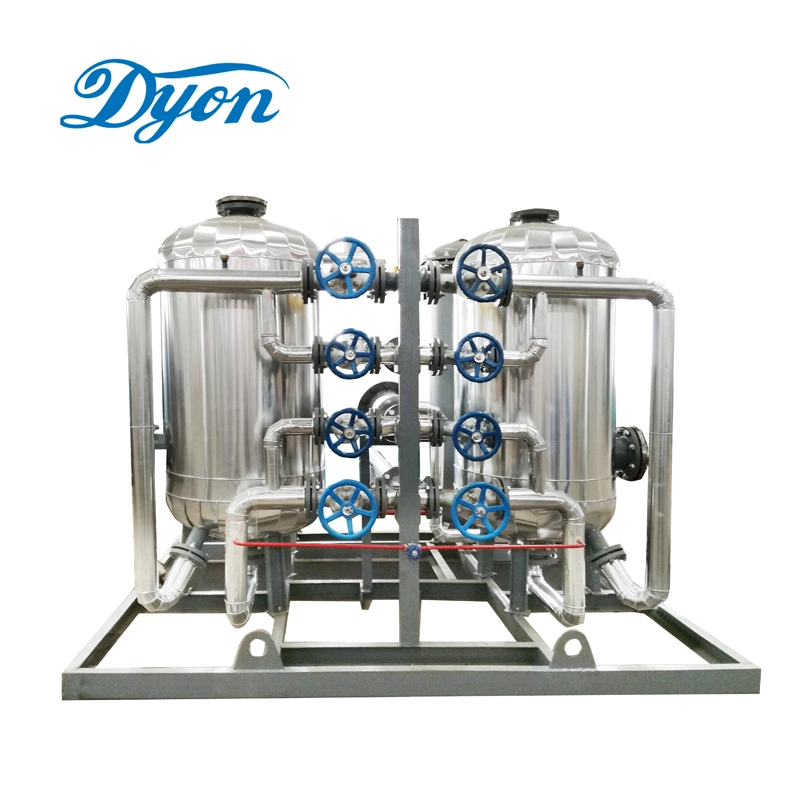
Air compressor
The inlet air will be compressed into the pressure as per process required.
It is sprayed-oil screw compressor, box-body construction, it have low noise, whole machine gather gas, lubricate, water, electric, cooling and instrument to one, realize machine and electric become one body.
Pre-cooling unit
The outlet temperature of compressed air is around 40ºC which is too high for the down-stream molecular sieves high efficiency operation, in order to increase the performance of the molecular sieves, a pre-cooling unit is required.
Purifier
Remaining contaminants in the process air such as moisture, carbon dioxide, acetylene (and etc.) shall be removed before enters into the main heat exchanger, a molecular sieves system is adopted.
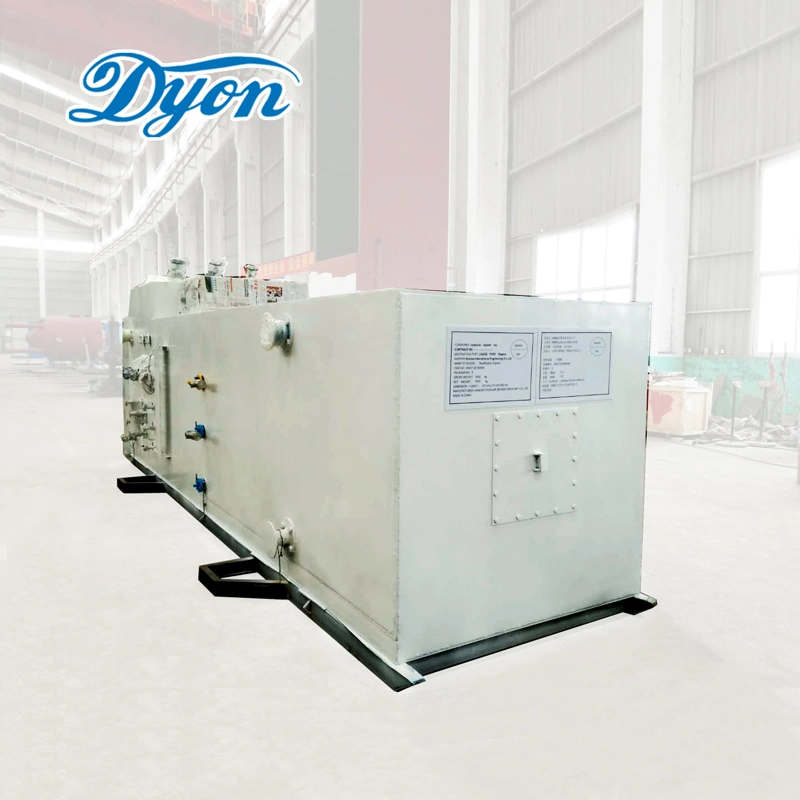
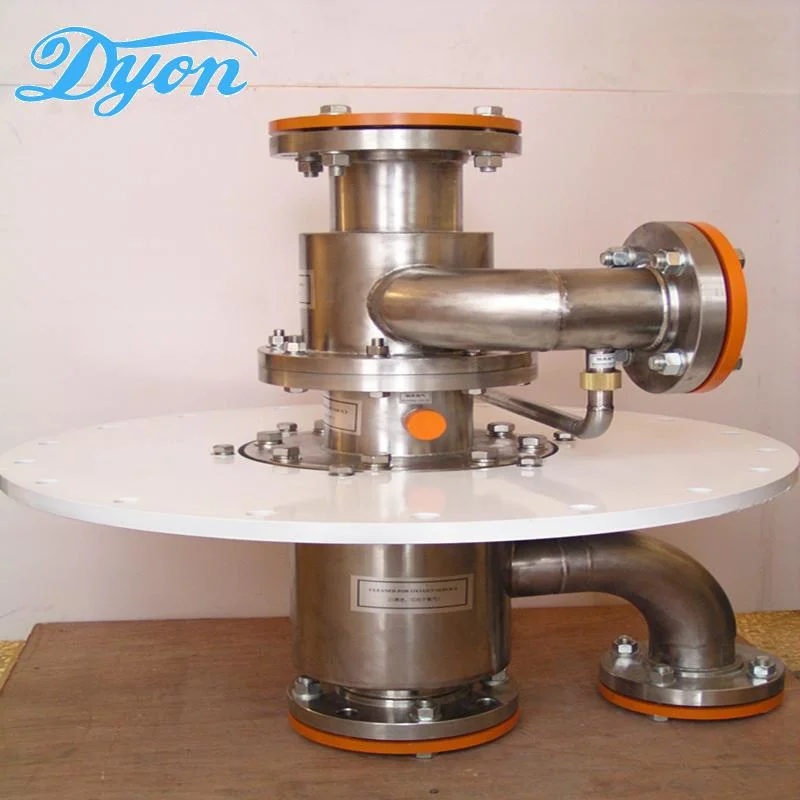
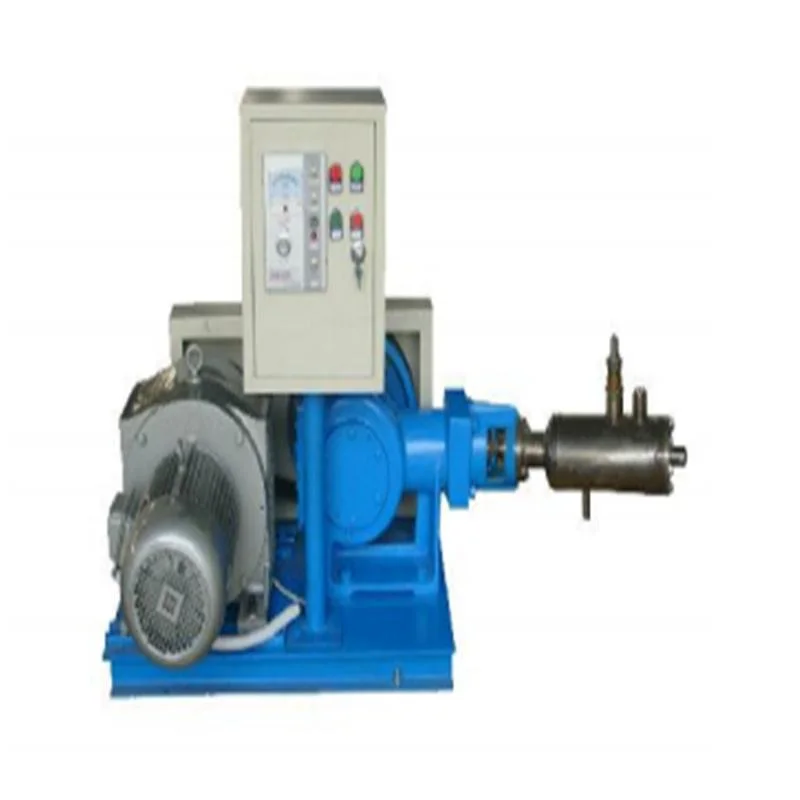
Fractionating column
It adopt fin type heat exchange, made in aluminum, heighten heat exchange affection, depress the operating pressure, reduce the power consumption furthest, saving cost.
Turbine expander
Turbine expander also referred to as a turbo-expander, is a centrifugal or axial-flow turbine, through which a high-pressure gas is expanded to produce work. It's the one of core part of the whole plant.
Liquid pump
Liquid pump is a kind of cryogenic liquid pump, by which the pressure of oxygen/nitrogen can be increased to achieve the purpose of transporting oxygen.
- All unit machines are skid-mounted construction, connected by fixed-size short pipe, it's not complicated to install.
- Adopt liquid oxygen pump inner-compress technology, could produce high-quality oxygen, which can be used both for medical and industrial filed.
- Complete set plant runs stablly, and it's easy to operate, convenient to maintenance, and we supply a two-year spare parts freely.
- Set four-stage pipeline oil-removing filter with imported filter element. Each filter element shall be replaced with a
monitor to remind users to replace the filter element regularly, preventing the
oil and water in the air from entering the purifier and fractionating tower. - Design and manufacture of the external cleaning tower system of the fractionating tower, no need open to clean the oil in the fractionating tower, avoiding the trouble of removing and reloading perlite, cutting and welding aluminum pipes and leak detection.
- All the fractionating tower is filled with waterproof pearlite (perlite), which ensures the start-up time of normal oxygen production due to its excellent cooling effect.
Advanced technology adopted in each unit can reduce power consumption greatly, and save electricity fee at the
same time.
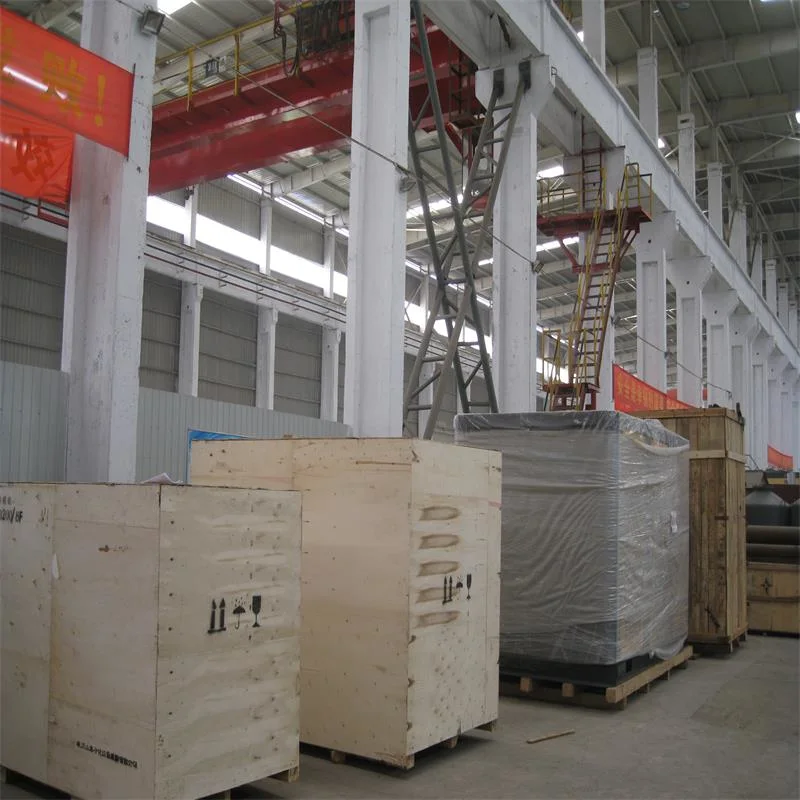
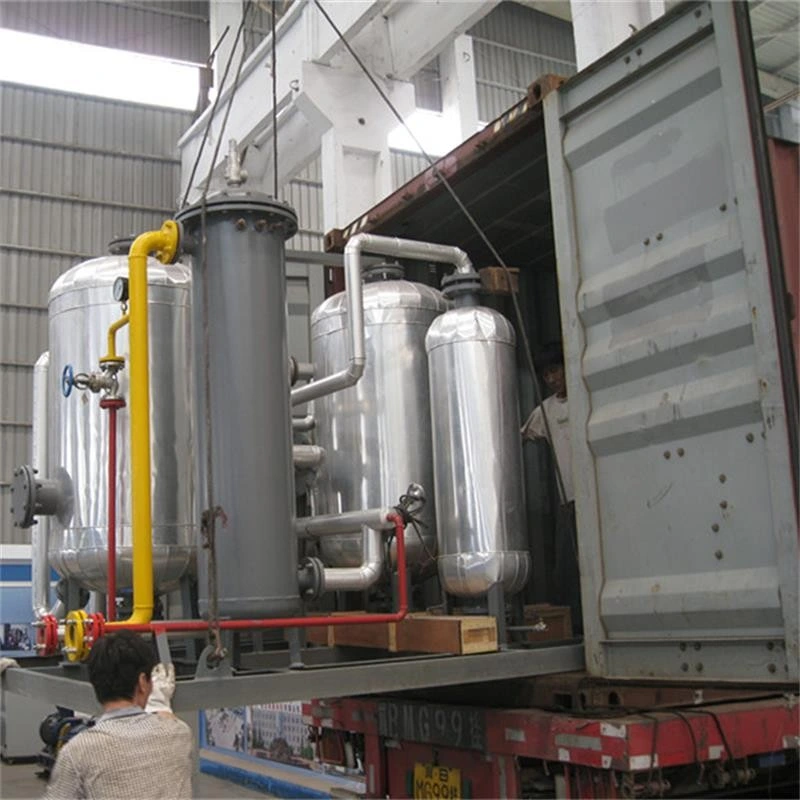

All goods are packed as required as transportation standard.
In order to improve equipment performance and provide customers with better products, our company has established a research and development center. After continuous research and creation, combined with market demand, we have invented many devices to improve equipment performance. The following is a partial display of our invention patent certificate:
Model | GO2 output and purity | GN2 output and purity | Unit power consumption | Occupied Area |
KZO-20 | 20Nm3/h, ≥99.6% | -- | 1.4KWH/NM3 O2 | ~100M2 |
KZO-30 | 30Nm3/h, ≥99.6% | -- | 1.4KWH/NM3 O2 | ~100M2 |
KZON-30/30 | 30Nm3/h, ≥99.6% | 30Nm3/h, ≥99.999% | 1.4KWH/NM3 O2 | ~100M2 |
KZO-40 | 40Nm3/h, ≥99.6% | -- | 1.4KWH/NM3 O2 | ~150M2 |
KZON-40/40 | 40Nm3/h, ≥99.6% | 40Nm3/h, ≥99.999% | 1.4KWH/NM3 O2 | ~150M2 |
KZO-50 | 50Nm3/h, ≥99.6% | -- | 1.4KWH/NM3 O2 | ~150M2 |
KZON-50/50 | 50Nm3/h, ≥99.6% | 50Nm3/h, ≥99.999% | 1.4KWH/NM3 O2 | ~150M2 |
KZO-80 | 80Nm3/h, ≥99.6% | -- | 1.38KWH/NM3 O2 | ~150M2 |
KZON-80/80 | 80Nm3/h, ≥99.6% | 80Nm3/h, ≥99.999% | 1.38KWH/NM3 O2 | ~150M2 |
KZO-100 | 100Nm3/h, ≥99.6% | -- | 1.38KWH/NM3 O2 | ~210M2 |
KZON-100/100 | 100Nm3/h, ≥99.6% | 100Nm3/h, ≥99.999% | 1.38KWH/NM3 O2 | ~210M2 |
KZO-120 | 120Nm3/h, ≥99.6% | -- | 1.38KWH/NM3 O2 | ~210M2 |
KZON-120/120 | 120Nm3/h, ≥99.6% | 120Nm3/h, ≥99.999% | 1.38KWH/NM3 O2 | ~210M2 |
KZO-160 | 160Nm3/h, ≥99.6% | -- | 1.3KWH/NM3 O2 | ~250M2 |
KZON-160/160 | 160Nm3/h, ≥99.6% | 160Nm3/h, ≥99.999% | 1.3KWH/NM3 O2 | ~250M2 |
KZO-180 | 180Nm3/h, ≥99.6% | -- | 1.3KWH/NM3 O2 | ~250M2 |
KZO-200 | 200Nm3/h, ≥99.6% | -- | 1.3KWH/NM3 O2 | ~250M2 |
KZO-250 | 250Nm3/h, ≥99.6% | -- | 1.3KWH/NM3 O2 | ~250M2 |
KZO-300 | 300Nm3/h, ≥99.6% | -- | 1.3KWH/NM3 O2 | ~250M2 |
KZO-350 | 350Nm3/h, ≥99.6% | -- | 1.3KWH/NM3 O2 | ~250M2 |